Mass production of microvalves could see advancement of microfluidic devices
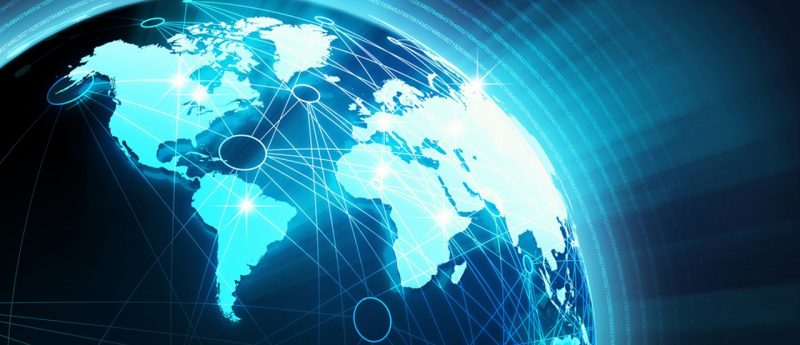
Researchers from the A*STAR Singapore Institute of Manufacturing Technology (SIMTech) have developed an air-actuated microvalve and micropump that can be utilized as functional elements for rapid integration in plug-and-play microfluidic devices. The team published their new developments in a recent paper in Microfluidics and Nanofluidics.Advances in microfluidic lab-on-a-chip technologies have presented a number of opportunities to researchers, particularly in providing the benefits of miniaturization, integration and automation in the context of immediate point-of-care diagnosis of diseases.
Microfluidic systems are increasingly useful in clinical applications including recently in stem cell studies and drug discovery. However, one of the obstacles for its successful application in diagnosis is the challenge of manufacturing miniature microfluidic components.
Zhenfeng Wang and colleagues at A*STAR Singapore Institute of Manufacturing Technology (SIMTech) have developed reliable microfluidic components that can be independently mass produced and fully integrated in microfluidic devices.
The development of mass producing a microvalve unit separately is hoped to aid in the manufacture of simpler and more robust microfluidic devices, which can be easily accessible for point-of-care diagnostic.
“Integrating valves and pumps into thermoplastic devices is usually challenging and costly because the fabrication process is very complicated,” commented Wang. “Mass-producing the microvalve module separately from the main device, however, makes the fabrication of the main device relatively simple and robust.”
The team developed a micropump compromising three microvalves – these microvalves consist of a flexible diaphragm inserted between a control and liquid chamber. Control of fluidic flow within the chamber is enabled by applying pressure to the diaphragm.
Wang and his colleagues used thermoplastic polyurethane film, a polymer, to overcome the challenges of finding a suitable material for designing the microvalve.”We found that thermoplastic polyurethane film works well as the membrane and can be bonded tightly with the main body, which is made from polymethyl methacrylate,” explained Wang.
The team applied a numerical tool to construct guidelines to design the microvalve structure, which was then corroborated with further experimentation.
Presently, the team are developing other ‘on chip’ units and are looking to advance capabilities of polymer-based microfluidic devices.
“Further miniaturizing the size of microvalve modules could increase the scale of integration and broaden the range of potential applications,” added Wang.
Sources: Shaegh SAM, Wang Z, Ng SHet al. Plug-and-play microvalve and micropump for rapid integration with microfluidic chips. Microfluids and Nanofluids 19(3), 557– 564 (2015); Small devices make a big impact.